Understanding the Role of Tube Fittings Manufacturers
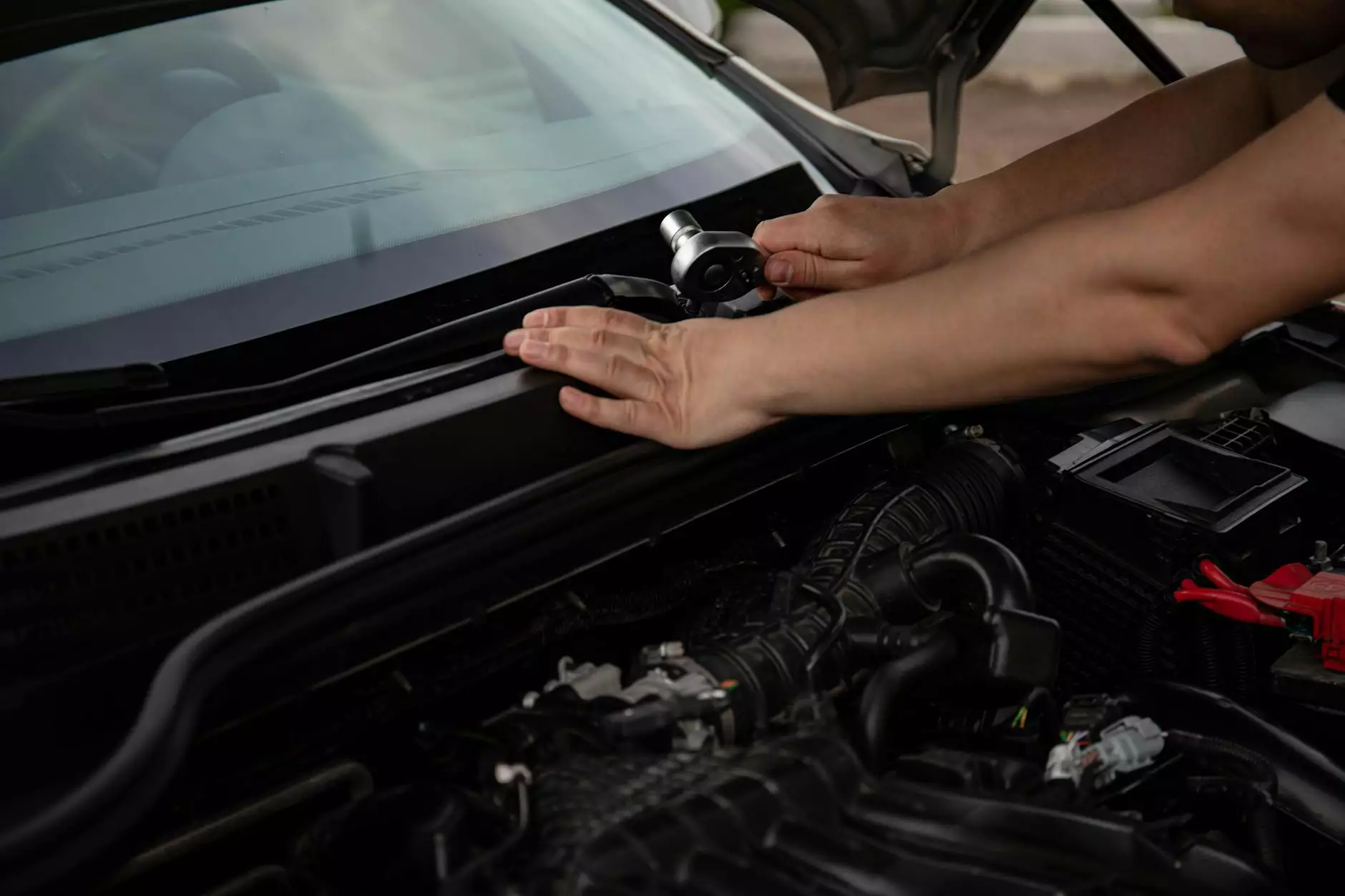
In the modern industrial landscape, tube fittings manufacturers play an essential role in the seamless functioning of a variety of systems. With a focus on quality, precision, and efficiency, these manufacturers provide an array of products that cater to diverse industrial needs. From tube fittings to valves and flanges, each component is crucial in ensuring optimal performance and safety in applications ranging from chemical processing to oil and gas industries. In this comprehensive article, we will delve deeply into the significance of tube fittings, the manufacturing processes, and the leading products offered by trusted manufacturers like Techtubes.
What Are Tube Fittings?
Tube fittings are mechanical components designed to connect tubes in a variety of systems. They ensure a leak-free and secure connection, enabling the efficient transport of fluids or gases. The proper fitting maintains the integrity of the entire system, minimizing the risk of failure. Tube fittings are pivotal in sectors such as:
- Aerospace
- Automotive
- Oil and Gas
- Pharmaceuticals
- Chemical Processing
The Importance of Quality in Tube Fittings
The quality of tube fittings can greatly affect the performance and safety of a system. Here are specific reasons why high-quality manufacturing is vital:
- Reliability: Reliable fittings reduce the chances of leaks, which can be catastrophic in various industries.
- Durability: Quality materials and manufacturing processes ensure that fittings can withstand pressure and environmental stress.
- Efficiency: High-performance fittings facilitate smooth operations, which in turn enhances the overall efficiency of the system.
- Compliance: Adhering to industry standards is crucial; quality manufacturers often meet or exceed these requirements.
Categories of Products Offered by Tube Fittings Manufacturers
Tube fittings manufacturers provide a wide range of products. Below, we discuss in detail the categories offered by companies like Techtubes.
1. Tube Fittings
Tube fittings can be categorized into different types, including:
- Double Ferrule Tube Fittings: Known for their reliable connection, these fittings are ideal for high-pressure applications.
- Single Ferrule Tube Fittings: These fittings offer a simpler connection method and are often used in low-pressure systems.
- NPT Fittings: National Pipe Taper (NPT) fittings are engineered for precision threading and provide robust sealing in pipe connections.
2. Ferrule Fittings
Ferrule fittings complement tube fittings by providing additional strength and security. They are essential in systems where tubes need to be connected safely without the risk of disconnection or leakage.
3. Forged Pipe Fittings
Forged fittings are manufactured from a solid piece of material, offering superior strength compared to cast fittings. They are suitable for high-pressure and demanding applications.
4. Threaded Pipe Fittings
These fittings are designed for easy assembly and disassembly. They are ideal for oily or corrosive environments where regular maintenance is needed.
5. Flanges
Flanges provide robust connection points at the end of piping systems. Available in various materials and sizes, they serve a key function in pressure management and system integrity.
6. Valves
Valves control the flow of fluids within piping systems. Manufacturers offer various types, including:
- Check Valves: Prevent reverse flow, ensuring that fluids flow in only one direction.
- Ball Valves: Provide reliable shut-off and control, making them a staple in flow regulation.
- Needle Valves: Offer fine control of fluid flow and pressure, commonly used in laboratory and instrumentation setups.
- Manifold Valves: Allow multiple connections and facilitate monitoring and control of flow and pressure.
Choosing the Right Tube Fittings Manufacturer
Selecting a reliable tube fittings manufacturer is crucial for ensuring the integrity and safety of your systems. Below are factors to consider:
- Experience: A manufacturer with extensive industry experience can better understand and meet your specific needs.
- Certifications: Look for manufacturers that have quality certifications, ensuring their products meet industry standards.
- Product Range: A broad product range indicates the manufacturer’s capability and expertise in meeting diverse requirements.
- Customer Support: Good customer support is essential for troubleshooting and assistance post-purchase.
The Manufacturing Process of Tube Fittings
1. Material Selection
The choice of material is paramount in ensuring the longevity and performance of tube fittings. Common materials include:
- Stainless Steel: Known for its corrosion resistance and strength.
- Brass: Offers good corrosion resistance and is often used in plumbing applications.
- Carbon Steel: Provides strength and is often used for high-pressure applications.
- Plastic: Used in specific applications where corrosion resistance is necessary.
2. Precision Machining
Once the material is selected, precision machining is employed to create exact dimensions for the fittings. This involves:
- Turning
- Milling
- Drilling
3. Quality Control
Quality control processes are implemented at every stage of manufacturing. This includes:
- Visual inspections
- Dimensional checks
- Pressure testing
4. Surface Treatment
Surface treatments enhance the fittings' resistance to corrosion and wear. Common treatments include:
- Galvanization
- Passivation
- Coating
Applications of Tube Fittings
Tube fittings find applications across various industries. Some notable examples include:
- Hydraulic Systems: Facilitate the transfer of hydraulic fluid, enabling the operation of machinery and vehicles.
- Pneumatic Systems: Serve to transport compressed air, essential for actuators and control components.
- Food and Beverage: Used in piping and processing systems requiring sanitary conditions and regular cleaning.
- Cooling Systems: Essential in the transport of coolant fluids, ensuring efficiency in machinery and systems.
Future Trends in Tube Fittings Manufacturing
The industry is evolving with technological advancements. Future trends to watch include:
- Smart Fittings: Innovations such as IoT integration for monitoring flow and pressure.
- Advanced Materials: The use of lightweight and highly durable materials.
- Sustainable Manufacturing: Increased focus on eco-friendly practices and materials.
Conclusion
In conclusion, the role of tube fittings manufacturers like Techtubes is pivotal in various industries, providing critical components that ensure system reliability and efficiency. As technology advances, the focus on quality, safety, and sustainability will continue to shape the industry. Choosing the right manufacturer is essential for achieving optimal performance, and at Techtubes, we are committed to providing innovative solutions that meet the evolving needs of our customers.
For high-quality tube fittings and related products, Techtubes is your trusted partner. Contact us today to learn more about our products and how we can assist you in your industrial needs.