Understanding Electric Injection Molding Machines: The Future of Manufacturing
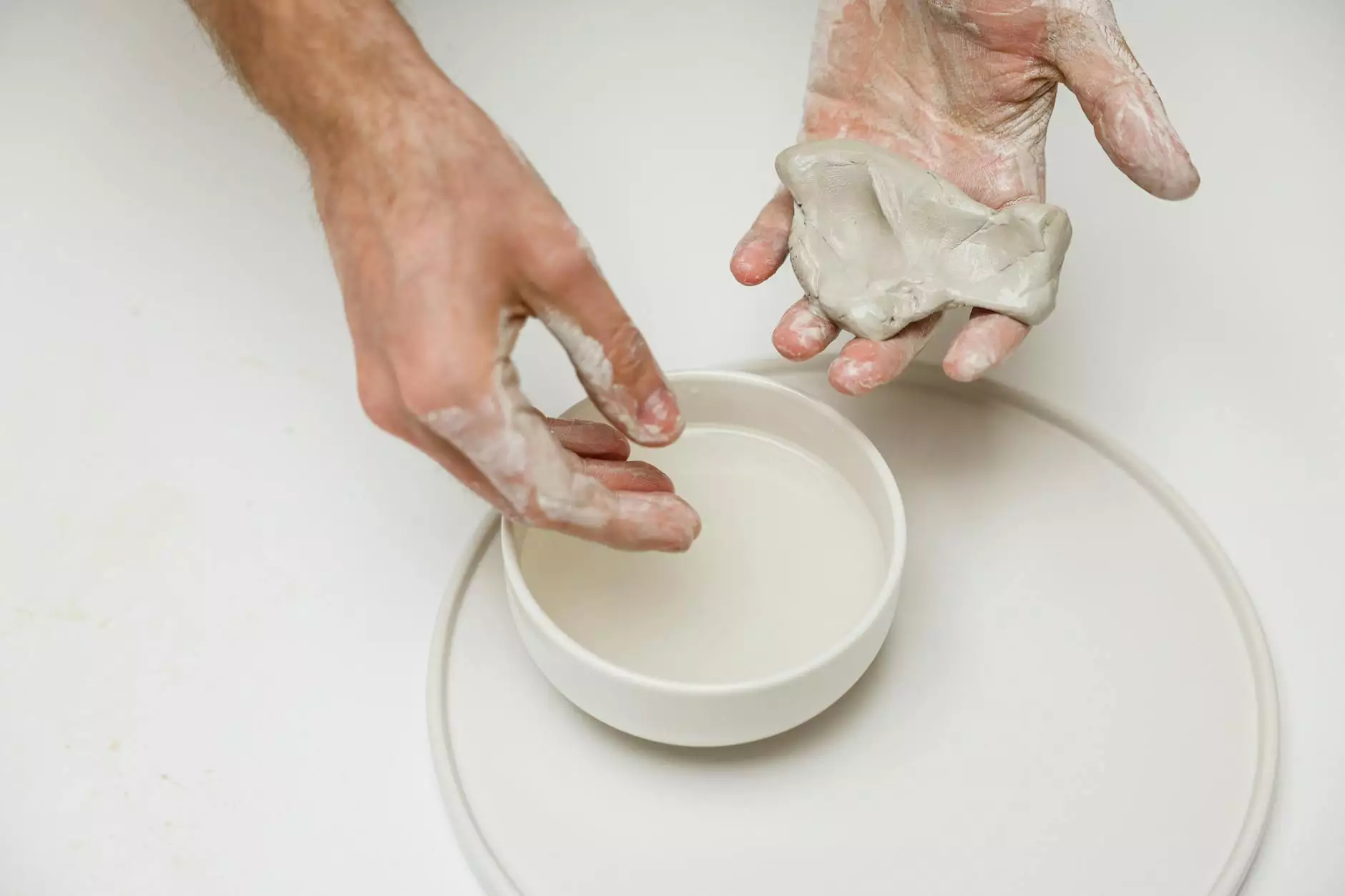
The manufacturing industry has seen significant advancements over the years, particularly with the introduction of cutting-edge technology that enhances efficiency and precision. Among these innovative solutions, the electric injection molding machine stands out as a transformative apparatus that is revolutionizing the way products are produced. In this comprehensive article, we will explore the workings of electric injection molding machines, their benefits, applications, and how they are shaping the future of manufacturing, especially for businesses like Deep Mould in the metal fabricators sector.
What Is an Electric Injection Molding Machine?
An electric injection molding machine is a type of machinery used for manufacturing plastic products through a process called injection molding. This machine utilizes electrical energy rather than hydraulic systems to facilitate the injection process. It incorporates advanced technologies to provide improved precision, energy efficiency, and control compared to traditional hydraulic machines.
The Mechanism Behind Electric Injection Molding
The basic operation of an electric injection molding machine involves several sequential steps:
- Preparation: Raw plastic pellets are fed into the hopper where they are heated until they melt.
- Injection: The molten plastic is injected into a mold using a screw or plunger mechanism operated by electric servo motors.
- Cooling: The plastic is allowed to cool and solidify inside the mold.
- Demolding: Once solidified, the mold opens, and the finished product is ejected.
Key Advantages of Electric Injection Molding Machines
Electric injection molding machines offer a myriad of benefits that make them an attractive option for manufacturers. Here are the most significant advantages:
1. Energy Efficiency
One of the most compelling benefits of electric injection molding machines is their energy efficiency. These machines consume less energy compared to hydraulic machines because they rely on electric motors, which operate more efficiently than hydraulic pumps. This efficiency not only translates to lower energy bills but also contributes to a more sustainable manufacturing process.
2. Precision and Consistency
Electric injection molding machines provide exceptional precision in the injection process. The use of servo motors allows for precise control over the injection speed and pressure, resulting in consistent product quality. This is particularly important in industries where product dimensions and tolerances are critical.
3. Faster Cycle Times
Manufacturers benefit from faster cycle times due to the quick response and movement of electric components. The rapid transition between injection and cooling phases leads to increased productivity, allowing businesses to meet demand effectively without compromising quality.
4. Reduced Maintenance Costs
Electric systems typically require less maintenance than hydraulic systems. The absence of oil and hydraulic components in electric injection molding machines means fewer leaks, lower wear and tear, and diminished maintenance costs over time.
5. Enhanced Safety Features
With the reduction of hydraulic fluids, there’s a notable decrease in the safety hazards associated with traditional machines. Electric injection molding machines often come equipped with advanced safety features that help protect operators and the manufacturing environment.
Applications of Electric Injection Molding Machines
Electric injection molding machines are versatile and applicable in various industries, including:
- Consumer Electronics: Used for producing components like housings and connectors.
- Automotive: Essential for making precise parts critical to vehicle performance.
- Medical Devices: Manufacturing disposable products and intricate components requiring high precision.
- Packaging: Creating containers and other packaging solutions effectively.
The Future of Electric Injection Molding Machines
As technology continues to evolve, electric injection molding machines are expected to play an even more significant role in the future of manufacturing. Here are a few trends shaping their advancement:
1. Automation and Smart Manufacturing
The integration of IoT (Internet of Things) in manufacturing will drive the evolution of electric injection molding machines. Smart machines equipped with sensors and data analytics will allow manufacturers to optimize production processes, reducing waste and enhancing efficiency.
2. Sustainability Trends
With increased focus on sustainability, electric injection molding machines align perfectly with eco-friendly initiatives. Their energy efficiency combined with the potential for using recycled materials in the injection process can help manufacturers reduce their carbon footprint.
3. Customization and Flexibility
The demand for custom products is rising, and electric injection molding machines can offer the flexibility needed to cater to varied client needs without compromising speed or quality. This adaptability positions them favorably in a competitive manufacturing landscape.
Conclusion
In conclusion, the electric injection molding machine represents a significant leap forward in manufacturing technology. With benefits such as enhanced efficiency, precision, lower operational costs, and increased safety, these machines are well-suited to meet the demands of modern industries. As businesses like Deep Mould embrace these innovations within the metal fabricators sector, the future looks bright for electric injection molding machines. Their role in shaping sustainable, efficient, and high-quality manufacturing processes cannot be overstated.
In an ever-evolving market, it is essential for manufacturers to stay updated on the latest technologies, like electric injection molding, to maintain a competitive edge and meet customer expectations for quality and sustainability.