Unlocking the Potential of China Plastic Injection Moulding for Metal Fabricators: A Complete Industry Guide
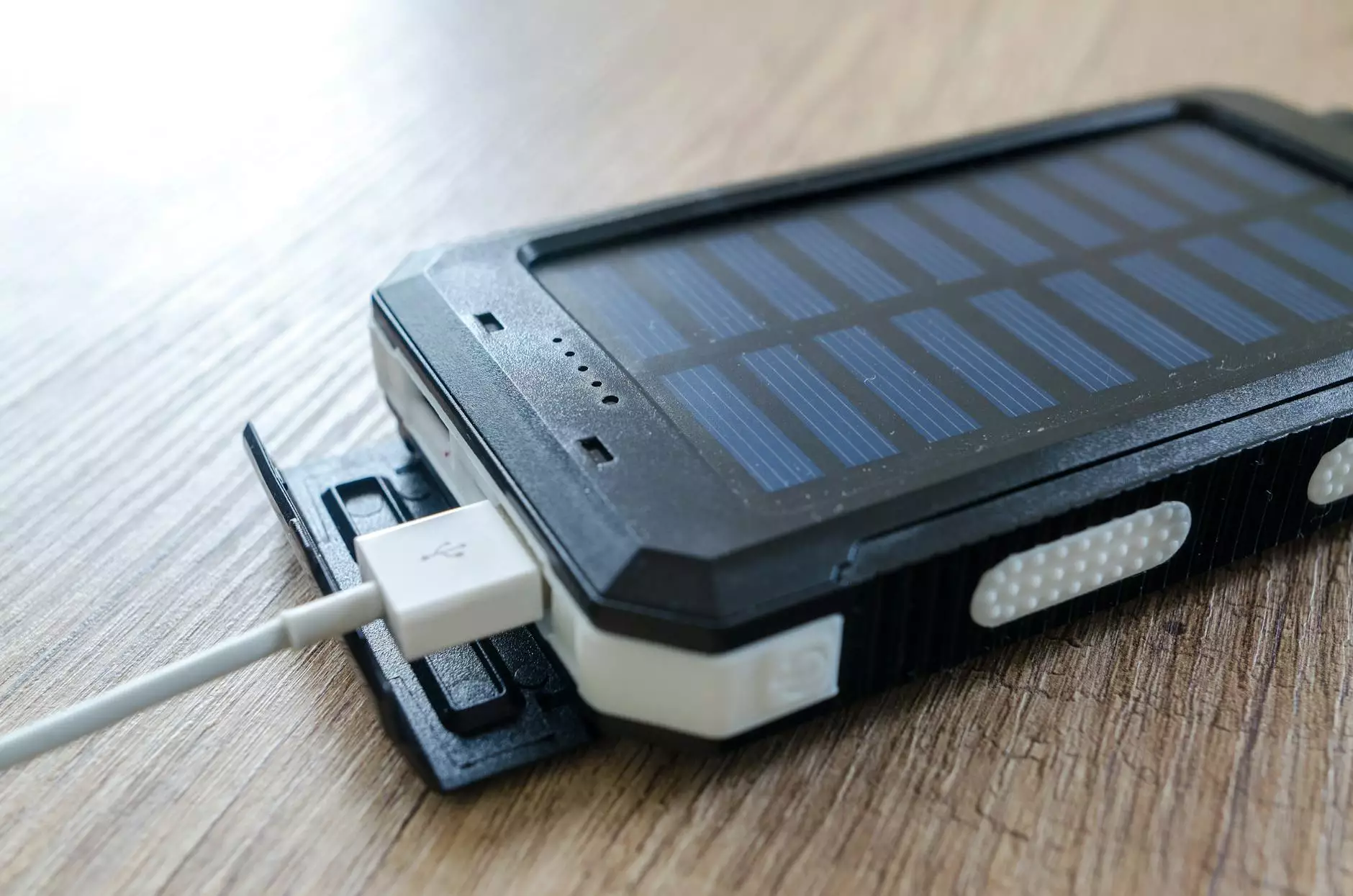
The manufacturing landscape is continuously evolving, driven by technological innovations and shifting market demands. Among the most transformative developments is the integration of China plastic injection moulding into various industries, notably metal fabricators. As a leading producer in this domain, DeepMould offers cutting-edge solutions that combine precision, efficiency, and cost-effectiveness.
Understanding China Plastic Injection Moulding and Its Significance in Metal Fabrication
China plastic injection moulding is a highly advanced manufacturing process wherein molten plastic is injected into precise molds to create intricate components. While traditionally associated with plastics, its integration with metal fabrication processes has opened new avenues for component manufacturing, especially in the realm of producing complex, functional parts with high detailed accuracy.
For metal fabricators, adopting this technology presents multiple benefits, including enhanced production capabilities, improved product quality, and increased operational efficiency. The synergy between plastic injection moulding and metal fabrication enables manufacturers to innovate with hybrid parts, durable composites, and lightweight assemblies, satisfying the demanding needs of contemporary industries such as automotive, aerospace, electronics, and consumer goods.
Why Metal Fabricators Should Embrace China Plastic Injection Moulding
The integration of china plastic injection moulding offers a significant competitive edge for metal fabricators. Here are the top reasons to consider this advanced manufacturing process:
- Cost Efficiency: Lower production costs due to China's competitive labour and manufacturing infrastructure, combined with high-volume production capabilities.
- Precision and Consistency: State-of-the-art mould designs allow for complex geometries with tight tolerances, ensuring consistent quality across batches.
- Fast Turnaround: Rapid mould fabrication and high-speed injection processes shorten lead times, accelerating product launch timelines.
- Design Flexibility: Ability to produce intricate features, internal cavities, and complex shapes that are challenging with traditional metal fabrication alone.
- Hybrid Manufacturing: Integration with metal components through multi-material assemblies or coatings, enhancing product functionality and aesthetics.
- Sustainable Practices: Use of recyclable plastics and energy-efficient processes contribute to greener manufacturing operations.
The Process of China Plastic Injection Moulding in Metal Fabrication
The china plastic injection moulding process tailored for metal fabricators involves several meticulously planned steps:
- Design and Engineering - Creating precise 3D models and prototypes utilizing CAD/CAM software to ensure accurate mold design that complements existing metal parts.
- Prototype Development - Producing initial prototypes to validate design, fit, and function before mass production.
- Mold Fabrication - Crafting durable and high-precision molds typically using CNC machining, EDM, and other advanced manufacturing techniques, often sourced from China’s top mold manufacturers.
- Injection Moulding - Melting plastic pellets and injecting them under high pressure into the custom molds, followed by cooling and ejection.
- Assembly and Integration - Combining plastic components with metal parts through assembly lines, bonding, or other finishing techniques for the final product.
- Quality Control - Conducting rigorous inspections such as dimensional analysis, tensile testing, and visual checks to ensure defect-free products.
Key Applications of China Plastic Injection Moulding in Metal Fabrication
The convergence of china plastic injection moulding and metal fabrication is transforming multiple sectors by enabling the creation of hybrid components that marry durability with innovative design:
- Automotive Industry: Manufacturing lightweight interior parts, custom dashboards, and complex faceplates that require high precision.
- Aerospace Equipment: Producing high-performance, lightweight components with stringent safety and durability standards.
- Electronics: Creating casing and housing parts that protect sensitive technology, with seamless integration of plastic and metal elements.
- Medical Devices: Fabricating sterilizable, biocompatible parts with intricate geometries for superior device performance.
- Consumer Goods: Developing innovative, ergonomic products that benefit from multi-material designs combining plastic and metal.
Choosing the Right Partner for China Plastic Injection Moulding
To effectively leverage china plastic injection moulding, it is critical to partner with experienced manufacturers who understand the intricacies of working with metal fabricators. Here are the vital qualities to look for:
- Reputation and Experience: A proven track record in delivering high-quality, complex molds tailored for metal fabrication applications.
- Technical Expertise: Skilled engineers with deep knowledge of mould design, materials, and advanced manufacturing techniques.
- Quality Assurance: Certifications such as ISO 9001 ensure consistent quality standards.
- Customer Support: Responsive communication and collaborative approach for seamless project management.
- Cost and Delivery: Competitive pricing with reliable and timely delivery schedules, especially from leading Chinese mould suppliers.
DeepMould: Your Premier Partner in China Plastic Injection Moulding
DeepMould stands apart by offering specialized china plastic injection moulding services tailored specifically for metal fabricators seeking innovation, precision, and cost savings. Our strategic location, integration of cutting-edge technology, and dedicated expertise ensure your projects are executed with excellence from prototype to mass production.
With a comprehensive suite of services including custom mold design, rapid prototyping, and high-volume manufacturing, DeepMould supports businesses in scaling their operations efficiently. Our commitment to quality and customer satisfaction makes us a trusted partner for metal fabricators aiming to integrate plastic injection moulding into their product portfolio.
Advantages of Working with DeepMould for China Plastic Injection Moulding
- Innovative Solutions: We pioneer new moulding techniques and optimize processes to meet your specific needs.
- Cost-Effective Manufacturing: Leveraging China's manufacturing ecosystem to reduce costs without compromising quality.
- Customization & Flexibility: From design to execution, we adapt to your unique project specifications.
- Fast Turnaround: Our streamlined processes guarantee rapid delivery timelines.
- Quality & Certification: Adherence to international standards ensures reliable, long-lasting products.
The Future of China Plastic Injection Moulding in Metal Fabrication Industries
The future landscape of china plastic injection moulding in metal fabrication is promising. Emerging trends include the integration of Industry 4.0 principles, such as IoT-enabled manufacturing, automation, and smart mold designs that facilitate predictive maintenance and real-time quality monitoring. These advancements will further reduce costs, accelerate production cycles, and enhance product complexity.
Additionally, increasing focus on sustainable manufacturing practices—such as utilizing biodegradable plastics and energy-efficient moulding techniques—will position China as a leader in eco-friendly solutions, appealing to global markets' growing sustainability demands.
Conclusion: Embracing the Power of China Plastic Injection Moulding for Metal Fabricators
In today's competitive landscape, embracing china plastic injection moulding can significantly enhance the capabilities of metal fabricators. This advanced process delivers superior precision, flexibility, and cost advantages, empowering manufacturers to innovate and meet complex client demands effectively. Partnering with a reliable provider like DeepMould ensures your projects are executed with excellence, driving your business growth and industry success.
As industries evolve and the demand for multifunctional components rises, integrating plastic injection moulding into your metal fabrication processes is no longer optional—it's essential for staying ahead in a dynamic market. Invest in the right technology and partnerships today to unlock endless possibilities for your manufacturing enterprise.